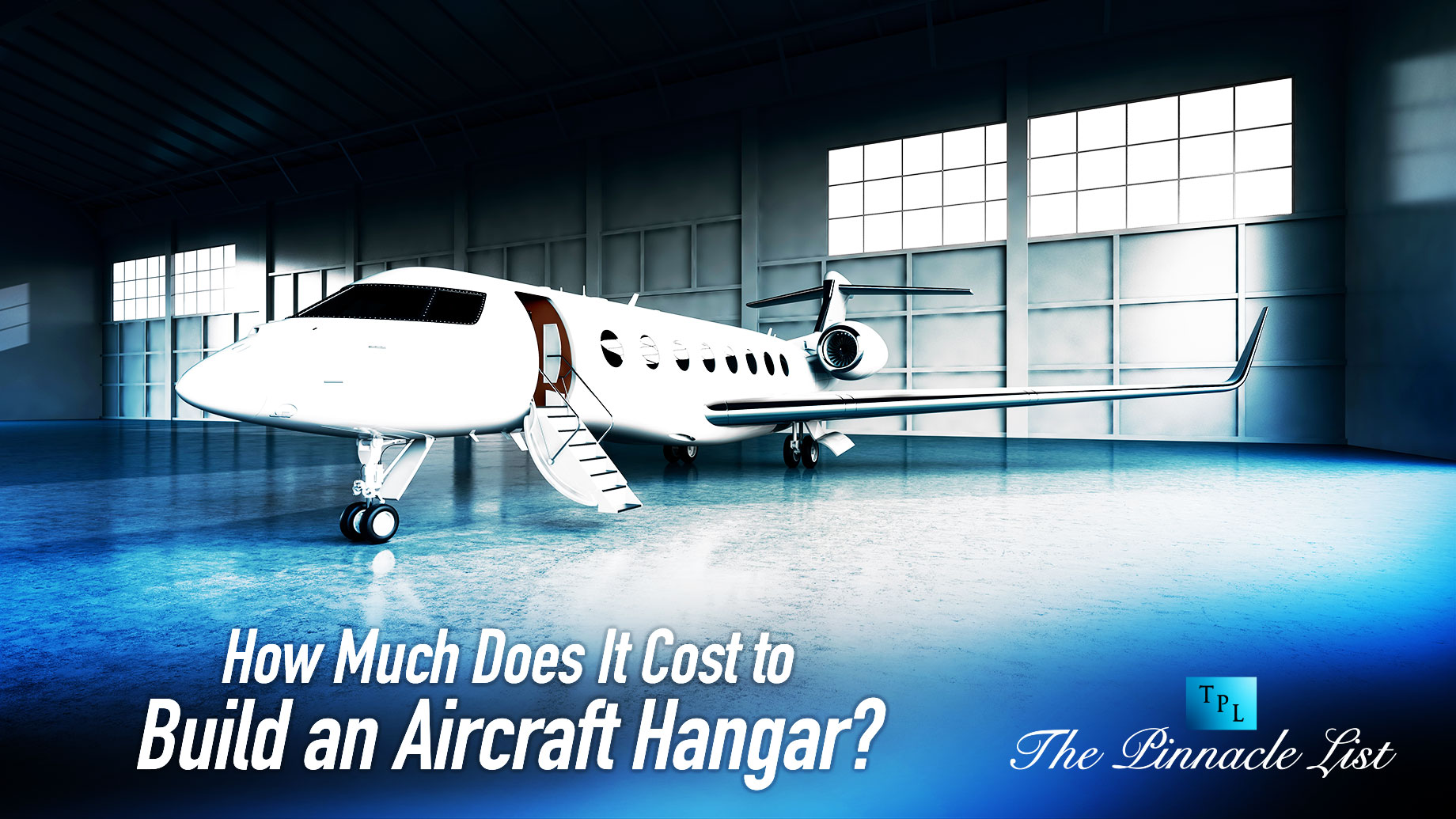
In the vast realm of aviation, the significance of an efficient airplane storage facility is often underplayed. These facilities, commonly known as aircraft hangars, serve as the frontline defense against external elements, providing much-needed protection to the valuable assets they shelter. Beyond their immediate role of housing airplanes, hangars also stand as a testament to an owner’s commitment to the longevity and maintenance of their aircraft.
However, like any infrastructural project, constructing an aircraft hangar doesn’t come without its considerations. Factors ranging from location and materials to customization and regulations play pivotal roles in determining the final construction budget.
Understanding the Different Types of Aircraft Hangars
Navigating the world of aircraft hangars can initially seem overwhelming, given the array of options available. Each type serves a distinct purpose, tailored to meet the diverse needs of the aviation community:
- T-hangars: These are the quintessential choices for single aircraft storage. Characterized by their ‘T’ shape, they are meticulously designed to accommodate individual aircraft, making them an efficient use of space and a favorite among private aircraft owners.
- Box hangars: When it comes to housing larger planes or an assortment of aviation equipment, box hangars emerge as the go-to. These spacious structures can cater to multiple aircraft and often come with additional areas for maintenance, storage, and operations, offering a comprehensive solution for commercial and private aviation enthusiasts alike.
- Shade hangars: For those seeking basic protection against direct sunlight, precipitation, or other elemental factors without the full enclosure, shade hangars offer a viable solution. These open structures, while not offering the comprehensive security of a closed hangar, provide adequate outdoor shielding, ensuring that the aircraft remains relatively safeguarded from harsh environmental conditions.
Factors Influencing the Cost of Building an Aircraft Hangar
The investment required to erect an aircraft hangar is shaped by a myriad of factors. It’s not simply about putting up four walls and a roof; it’s about crafting a safe, functional, and efficient space for one’s aviation assets. Here’s a deeper dive into the major components that sway the construction budget:
- Size and Dimensions: Naturally, the larger the hangar, the higher the associated costs. But it’s not just about square footage; ceiling height, door width, and overall design intricacies can influence the final price tag. Deciding on the capacity should be an amalgamation of current needs and future projections.
- Location: As with any real estate venture, location is paramount. Prime airport slots might command higher prices, but they also come with convenience. Further, local building codes and regulations can add layers of complexity and costs. Regional variances in labor rates, driven by demand and expertise, also play a role in the budgetary landscape.
- Materials: Steel remains a popular choice, revered for its durability and strength. Wooden structures, while exuding a rustic charm, might not offer the same lifespan. Meanwhile, modern composite materials, known for their resilience and weight efficiency, could come with a premium. The choice is a balance between longevity, aesthetics, and budget.
- Utilities and Amenities: A barebones hangar might fulfill basic storage needs, but integrating electrical systems, water connections, climate control, and security systems can drive up costs. Yet, these amenities also enhance functionality and ensure the longevity of the aircraft and equipment stored.
- Customization: Beyond basic storage, hangars can be personalized havens. Bi-fold doors can maximize space, tailored interiors can accommodate specific aircraft needs, and advanced security systems can offer peace of mind. Custom features, while enhancing user experience, will invariably impact the overall expenditure.
Average Aircraft Hangar Prices
Given the variables in play, hangar construction costs can vary significantly. However, market trends offer some guidance:
- Hangar Type Costs: On average, T-hangars might be the most economical, catering to single aircraft needs. Box hangars, with their expanded capacity and multi-functionality, will naturally demand a higher investment. Shade hangars, given their minimalist design, typically fall on the lower end of the spectrum.
- Cost Metrics: Standardizing costs per square foot or meter offers a tangible measure. While these metrics provide a ballpark figure, nuances like location, materials, and customization can cause deviations. It’s always prudent to gather multiple quotes and consult industry experts to gain a comprehensive financial picture.
Potential Additional Costs
Building an aircraft hangar is a significant investment, and while the upfront construction costs are often the primary focus, potential ongoing and peripheral expenses shouldn’t be overlooked:
- Regulatory Expenses: Before breaking ground, it’s essential to be familiar with the local zoning laws and airport regulations. Each airport might have its specific guidelines, and adhering to them might come with additional fees. From environmental assessments to safety clearances, the regulatory landscape can add layers of costs.
- Ongoing Maintenance: Every structure faces the inevitable wear and tear, and hangars are no exception. Whether it’s weather-induced corrosion or regular usage strain, maintenance costs can accumulate over time. Periodic inspections, repainting, or part replacements are realities to budget for.
- Insurance: Protecting your hangar and the invaluable aircraft within it is crucial. Insurance premiums can vary based on factors such as hangar location, construction materials, and the type and value of aircraft stored. It’s essential to shop around, understand coverage limits, and ensure both your hangar and aircraft are adequately protected.
Ways to Reduce Costs
While constructing an aircraft hangar is undeniably an investment, there are strategies to ensure the best value for your money:
- Benefits of Prefabricated Hangars: Modern engineering has paved the way for prefabricated hangars that are not only quicker to set up but also generally more cost-effective. These modular structures, while being lighter on the pocket, don’t compromise on durability or functionality.
- Off-Season Construction: Just as with other industries, construction can have its peak and off-peak seasons. Building during off-season periods might allow for better labor rates and material deals, potentially shaving a percentage off the total costs.
- Hangar-Sharing: A growing trend, especially among private aircraft owners, is the concept of hangar-sharing. By splitting costs with fellow owners, one can benefit from a state-of-the-art hangar facility without bearing the full financial brunt.
Conclusion
Constructing an aircraft hangar is undeniably a monumental task, intertwining the quest for quality with the inevitable concerns of cost. With myriad factors to consider, from materials to regulatory nuances, achieving the optimal balance between durability, functionality, and cost-efficiency becomes paramount.
The aviation world is ever-evolving, with technology and trends shaping the way we think about aircraft storage and protection. In such a landscape, making informed decisions can significantly influence the longevity and efficacy of the investment.
Therefore, before embarking on this journey, the importance of seeking professional consultation cannot be overstated. Experts in the field bring invaluable insights, ensuring that every dollar spent is a step towards the ideal hangar for your aircraft. Moreover, obtaining multiple construction estimates provides a broader perspective, helping potential hangar owners navigate the financial landscape with clarity and confidence.
In the end, an aircraft hangar is more than just a storage facilityโit’s a testament to an individual’s or organization’s commitment to aviation excellence. And with the right approach, that commitment can manifest in a structure that stands the test of time, both in durability and design.