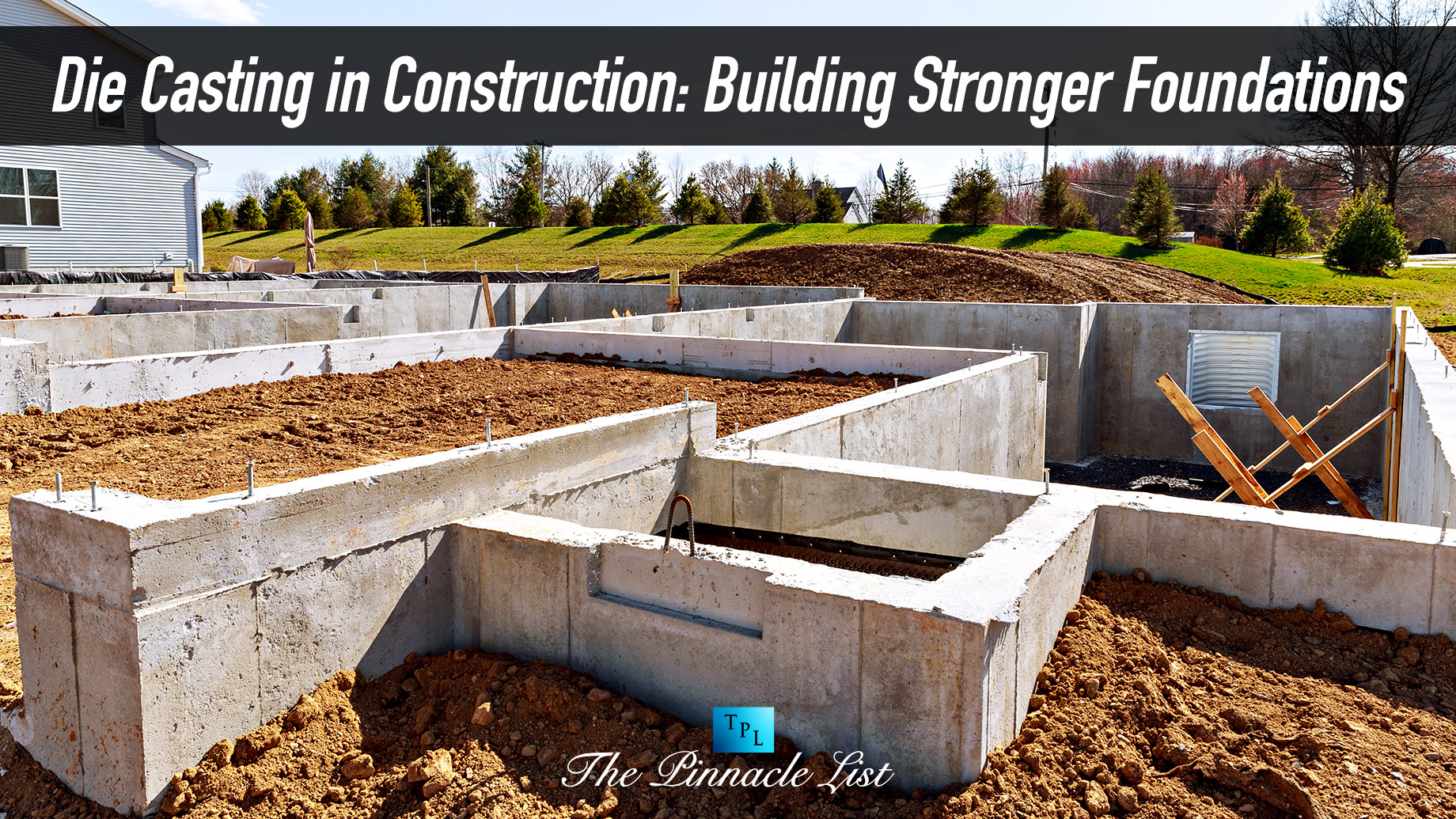
Understanding Die Casting in Construction
Die casting plays a key role in making parts for buildings. This process uses hot liquid metal to create strong, detailed pieces quickly. Let’s look at how it works, what materials are used, and the equipment needed.
Basics of Die Casting
Die casting makes metal parts by forcing melted metal into a mold. The mold is made of strong steel that can handle high pressure. When the metal cools, you get a finished part.
This method is great for making lots of the same part fast. It can create complex shapes with smooth surfaces. Die-cast parts often need little extra work after they come out of the mold.
In construction, die casting makes things like door handles, window frames, and other hardware. These parts are strong and look good. They can have fine details that other methods can’t make as well.
Materials Used in Die Casting
Die casting uses metals that melt easily. The most common ones are:
- Aluminum: Light and strong
- Zinc: Easy to work with and resists rust
- Magnesium: Very light but still tough
These metals flow well when hot. This helps them fill all parts of the mold. They also cool fast, which speeds up the process.
Each metal has its own good points. Aluminum is great for big parts that need to be light. Zinc is good for small, detailed parts. Magnesium works well for thin-walled pieces.
Die Casting Equipment and Machinery
Die casting needs special machines to work. The main parts are:
- The die: This is the mold that shapes the metal.
- The injection system: It pushes the melted metal into the die.
- The clamping system: It holds the die closed during casting.
The machines can be big or small. It depends on the size of the parts you’re making. Some are as big as a room!
The process starts by melting the metal. Then, the machine injects it into the die at high pressure. After the metal cools, the die opens, and the part comes out.
New tech helps make die casting even better. Computer controls make sure each part is just right. This is key for making building parts that fit perfectly every time.
Die Casting Techniques
Die casting uses special methods to make metal parts. These techniques shape molten metal into precise forms. Let’s explore the main types and processes used in die casting.
Types of Die Casting
There are two main types of die casting: hot chamber and cold chamber. Hot chamber works well for metals that melt at lower temps, like zinc. A cold chamber is better for metals that need higher heat, such as aluminum.
Hot chamber machines have a built-in furnace. This keeps the metal hot and ready to use. Cold chamber machines heat the metal separately. You then pour it into the machine for each part.
Both types make strong, detailed parts. But they suit different metals and production needs.
Pressure Die Casting Processes
Pressure die casting forces molten metal into a mold at high speed. This process has a few key steps:
- Melt the metal
- Inject it into the mold
- Let it cool and harden
- Open the mold
- Remove the part
The high pressure helps the metal fill every tiny space in the mold. This makes very precise parts with smooth surfaces.
Comparing Hot Chamber and Cold Chamber Processes
Hot chamber die casting is fast and works well for zinc, tin, and lead. The metal stays in the machine, so you can make parts quickly. But it’s not good for metals that melt at high temps.
Cold chamber is slower but can handle aluminum and other metals that melt at higher temps. You melt the metal outside the machine, then pour it in for each part. This takes more time but works for a wider range of metals.
Here’s a quick comparison:
Feature | Hot Chamber | Cold Chamber |
Speed | Faster | Slower |
Metals | Low melting point | High melting point |
Setup | Simpler | More complex |
Part size | Smaller | Larger possible |
You’ll choose based on the metal you’re using and how many parts you need to make.
Design Considerations for Die Casting
Good die casting design is key for strong, high-quality parts. You’ll need to think about the mold, part strength, and how the metal behaves as it cools. Let’s look at some important factors to keep in mind.
Mold Design and Mold Cavity
Your mold cavity shapes the final part. You want smooth surfaces and easy part removal. The parting line is where the mold halves meet. Put it where it won’t affect how the part looks or works.
Use draft angles on vertical walls. This helps the part come out of the mold easily. A good rule is 1-3 degrees of draft for most parts.
Add fillets to inside corners. This helps the metal flow better and makes stronger parts. Sharp corners can cause weak spots or cracks.
Incorporating Ribs and Holes for Strength
Ribs make parts stronger without adding too much weight. Space them evenly and keep them about 60% as thick as the main walls. This prevents sink marks on the surface.
You can cast holes directly into your part. But very small or deep holes might need drilling after casting. For cast holes, use a slight taper to help with mold release.
Ribs and holes also help control how the part cools. This can reduce warping and improve overall quality.
Managing Shrinkage and Wall Thickness
Metal shrinks as it cools in the mold. You need to account for this in your design. Different metals shrink at different rates. Ask your die caster for help with shrinkage rates.
Keep wall thickness as even as possible. This helps the part cool evenly and prevents warping. Aim for walls between 0.5 and 5 mm thick. Thicker areas can cause sink marks or take too long to cool.
If you need thick and thin areas, use gradual changes. This helps the metal flow better and cool more evenly. Good wall thickness design leads to stronger, better-looking parts.
Applications and Benefits
Die casting has many uses in construction and other industries. It offers some big advantages for making metal parts quickly and accurately.
Die Casting in the Automotive Industry
Car makers use die casting a lot. They make engine parts, transmission cases, and body components this way. Die cast parts are light but strong. This helps cars use less fuel.
You’ll find die cast parts in brakes, steering systems, and suspensions too. The process lets car makers make complex shapes easily. It also works well for making many identical parts fast.
Die casting is great for making thin-walled parts. This comes in handy for things like oil pans and valve covers.
Die Casting for Consumer Electronics
Your phone, laptop, and other gadgets likely have die cast parts. The cases for these devices are often made this way. Die casting works well for small, detailed parts.
It’s used for heat sinks in computers and TVs. These parts need good heat transfer. Die cast aluminum does this job well.
Game consoles and home appliances use die cast parts too. The process makes strong, light parts that look nice. This matters for things you see and use every day.
Advantages of Die Casting for Construction
In building, die casting has some big pluses. You get parts that are the same every time. This matters when pieces need to fit just right.
Die cast parts can handle heat well. This helps in places that get hot, like near engines or in sunny spots.
The parts are strong but not heavy. This makes them good for things like door handles, window frames, and light fixtures. You can make parts with thin walls but still keep them tough.
Die casting lets you add details right into the part. This can cut down on extra work later. It’s also good for making parts that won’t rust.
Post-Casting Operations and Finishing
Die casting parts need some extra steps after they come out of the mold. These steps make the parts look better and work properly. Let’s look at how the parts are cleaned up and cooled down.
Trimming and Surface Finish Techniques
Once you’ve cast your part, it might have extra bits of metal. You’ll need to trim these off. There are special tools for this job. They cut away the extra metal quickly and neatly.
After trimming, you’ll want to make the surface smooth. You can use grinding or polishing machines for this. They remove any rough spots. Some parts need a really shiny finish. For these, you might use buffing wheels.
Sometimes, you’ll need to add texture to the surface. This can make the part look nicer or help it work better. You can do this with special tools or chemicals.
Cooling and Ejection Systems
Your die cast parts need to cool down before you can use them. The mold has special channels for cooling liquid. This helps the metal harden faster.
Once the part is cool enough, it’s time to get it out of the mold. Ejector pins push the part out. These pins are part of the mold design. They help make sure the part comes out without getting damaged.
Some parts might stick to the mold. You can use a release spray to help with this. It makes it easier to get the part out without scratching it.