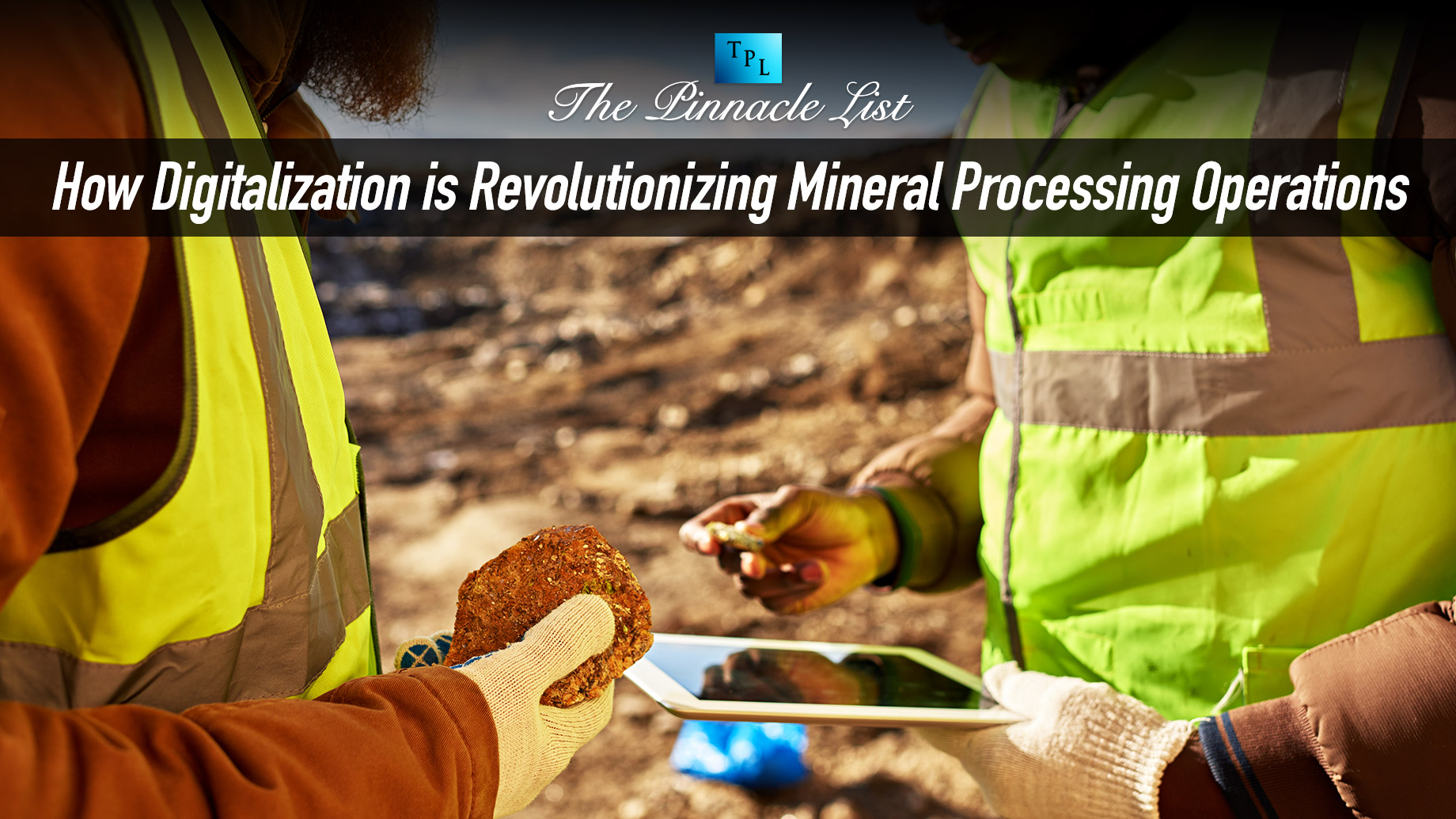
Globalization is intensifying and changing the overall course of industries, and the mining industry has not remained immune. In mineral processing operations, digital technologies are nowadays becoming useful in increasing efficiency and safety and in cutting down costs. In this article, the author seeks to understand how the essence of mineral processing is being changed through digitalization with an emphasis on the technologies. The findings are directed to firms within the mining industry that require advice on how digital improvement will benefit them.
Enhancing Equipment Efficiency
Perhaps one of the most important advantages of digitalization across the mineral processing industry is the enhancement of equipment utilization. Smart technologies mean that the performance of machinery can be monitored in real time to identify trends that can be indicative of a forthcoming failure, thus preventing such incidents.
For example, sand processing equipment may include digital sensors that are used to monitor some of the factors, such as vibration, temperature, or pressure, in the production process, as well as useful information that may be used to enhance production performance. Such insights make it easier to control the operation conditions and thereby minimize usage or setup while enhancing its shelf life.
In addition, digital twin, a virtual copy of the real equipment, enables the estimation of processing conditions using simulation technologies. This technology assists the firms in practicing various conditions and operations in simulation, improving their functionality, and minimizing operational hazards without interfering with the actual manufacturing.
Real-Time Data and Analytics
Advancements in technology, specifically digital technology, have brought real-time data collection and analysis to the process of mineral processing. The technology involves the use of sensors that are installed on processing equipment, and they gather huge amounts of data; the data is analyzed with the help of efficient algorithms to get useful information.
For instance, in operations with a portable cone crusher, real-time data can also be applied to track the rate at which material is being fed into the crusher, the power that is being consumed, and the proportions of content in the crushed material. Such data helps the operators to change some settings ahead to enhance crushing efficiency besides cutting some extra energy that tends to be used.
Moreover, real-time analytics will make it possible to discover patterns and trends that were earlier unnoticeable. Performing analysis of such data ensures that relevant decisions are made in order to increase productivity, minimize wastage, and formulate efficient processes.
Automation and Process Control
Automation is one of the major aspects of the digitization process in mineral processing. In the processing operation, it is possible for the systems involved to regulate their activities and aspects, such as materials movement and the operating of equipment in the process, thus decreasing the chances of human input and error.
Regarding portable cone crushers, there is always an opportunity to increase operational efficiency through the application of automation systems. By the use of other automatic controlling techniques, the parameters of the crusher may be controlled in real-time by Feed and product characteristics that are very significant in meeting the necessary product specification and increasing efficiency. This also enhances the efficiency of the system and, at the same time, has the advantages of energy saving and reduction in maintenance expenses.
Finally, several further improvements can be observed; more specifically, the advanced process control systems can compile data depending on the stages of the processing operation, which is beneficial as it offers an overall picture of the process. It also helps businesses make improvements throughout the extractive process up to the production of the final product, hence reducing costs.
Predictive Maintenance and Reduced Downtime
In the implementation of mineral processing, one of the most valuable benefits of digitalization is the ability to perform predictive maintenance. Advanced maintenance, also known as predictive maintenance, involves monitoring the information from the equipment and determining the probable time that a certain component is bound to fail; thus, preventive maintenance is done before the component fails.
The concept of predictive maintenance can especially be greatly helpful in the manufacture of sand processing equipment. As it is with the other components of the food processing line, screens, and conveyors, for instance, their condition can be checked by operators, and alerts made when they are worn out or damaged. This approach also prevents the occurrence of equipment breakdown and minimizes the expenses incurred to fix the equipment.
Secondly, predictive maintenance can be connected with an automatic system that activates maintenance signals and can also place an order for spare parts on its own. This helps everyone, especially the maintenance on administrative load, to provide equipment at optimal state at all times, thus improving the efficiency of the operation.
Sustainability and Environmental Impact
Digitalization is also at the forefront of highlighting several factors that may help increase the sustainability of mineral processing operations. Technological advancements in managing the internal operations of businesses ensure that the firms use resources efficiently by cutting wasteful processes while simultaneously delivering on the desired efficiency.
For instance, state-of-the-art monitoring equipment on portable cone crushers can help drive down energy use by guaranteeing that the unit is operating at optimum. Not only does this make operating expenses more affordable, but it ultimately shrinks the operation’s environmental impact as well.
However, there are benefits to the use of digital technologies as they result in optimum utilization of the resources. Through monitoring and data analysis, it is easy to have full control of the material flow in a timely manner with little or no wastage of resources. This leads to better and more efficient mining practices that are crucial in today’s economy and are conscious of the environment.
This entry illustrates that process intensification is evident in digitalization and gaining prominence in mineral processing operations. When implemented in the mining sector, technologies like real-time data analytics, automation, and predictive maintenance will enable businesses to seize more market share.
Thus, it is best for those involved in sand processing or using portable cone crushers to adapt to digital technologies. In this case, such tools also enhance the efficiency of equipment while at the same time supporting more sustainable and cost-effective approaches. Over time, more and more processes will be digitalized and the technology will start influencing the sector a lot more, thus it is to the advantage of every business to adapt and adopt the new change.