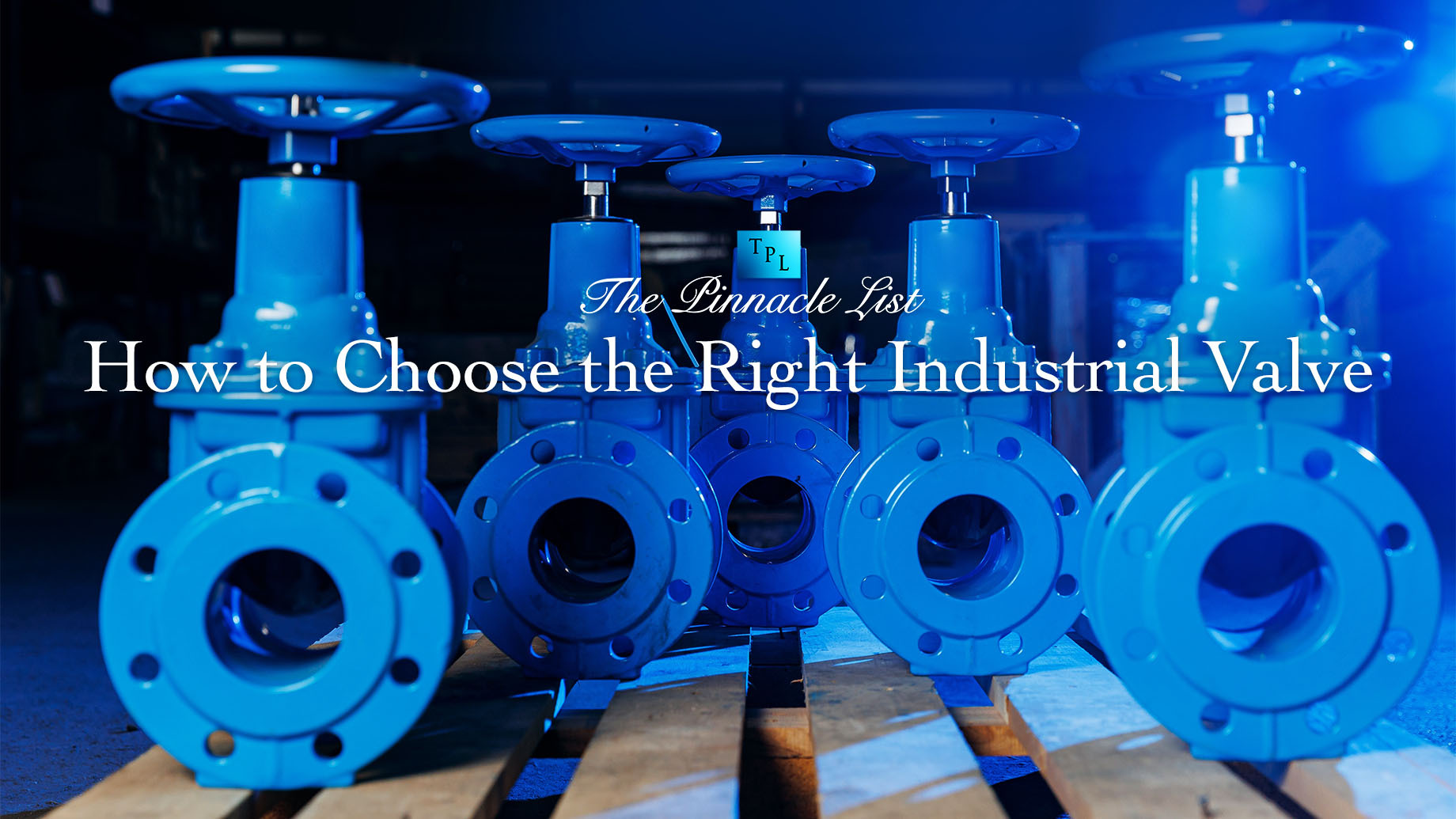
Industrial valves are essential components in a wide range of industries, from oil and gas to manufacturing and water treatment. They regulate, control, and direct the flow of fluids, gases, or slurries through a system. Selecting the right valve for your specific application can significantly impact efficiency, safety, and operational costs.
With numerous types and specifications available, choosing the right valve may seem overwhelming. This article will guide you through the key factors to consider when selecting an industrial valve.
1. Understand the Valve’s Purpose
The first step in choosing the right valve is identifying its primary purpose within your system. Different valves serve specific functions, including:
- On/Off Control: Valves like gate or ball valves are ideal for starting and stopping fluid flow.
- Flow Regulation: Globe or needle valves are suitable for precise control of flow rate.
- Pressure Control: Pressure relief or pressure-reducing valves ensure the system operates safely under specified pressure limits.
- Direction Control: Check valves prevent backflow and maintain one-way fluid movement.
Clearly defining the valve’s role helps narrow down your options.
2. Know Your Medium
The type of medium (fluid, gas, or slurry) that will pass through the valve is critical in determining the appropriate material and design. Key considerations include:
- Corrosive Fluids: Use valves made from corrosion-resistant materials like stainless steel, bronze, or PVC for handling acids or chemicals.
- High-Temperature Media: For extreme temperatures, consider valves with heat-resistant materials such as forged steel or alloys.
- Viscous or Solid-Laden Media: Slurries or thick fluids require valves with wider openings and durable seals, like plug or pinch valves.
Compatibility between the valve material and the medium ensures durability and optimal performance.
3. Assess Pressure and Temperature Requirements
Industrial valves are designed to handle specific pressure and temperature ranges. Operating a valve outside its rated limits can lead to failure, safety hazards, and costly downtime. Key factors to assess include:
- Maximum Pressure (PSI): Ensure the valve can withstand the highest pressure expected in your system.
- Temperature Tolerance: Verify the valve’s material and seals can endure the system’s maximum and minimum temperatures.
Refer to industry standards, such as ANSI or API specifications, to ensure compliance with safety and performance benchmarks.
4. Select the Right Valve Type
There are several types of industrial valves, each suited to particular applications:
- Gate Valves: Best for fully open or fully closed positions, often used in pipelines for isolation.
- Ball Valves: Provide excellent shutoff capabilities and are ideal for high-pressure systems.
- Globe Valves: Designed for precise flow regulation, commonly found in throttling applications.
- Butterfly Valves: Compact and cost-effective for regulating large flow volumes.
- Check Valves: Prevent reverse flow, ensuring unidirectional movement of fluids or gases.
- Diaphragm Valves: Suitable for systems requiring tight seals, often used in food, pharmaceutical, or chemical industries.
Selecting the right valve type depends on your operational needs and system design.
5. Consider Actuation Method
Valves can be manually operated or automated using different actuation methods:
- Manual Valves: Operated by handwheels, levers, or gears, suitable for systems that require infrequent adjustments.
- Electric Actuators: Offer precise and remote control, ideal for systems integrated with automation processes.
- Pneumatic Actuators: Use compressed air for quick and reliable operation, commonly found in industrial applications.
- Hydraulic Actuators: Provide high torque for heavy-duty valves in high-pressure systems.
Choose an actuation method based on the system’s level of automation, speed requirements, and accessibility.
6. Factor in Size and Flow Requirements
Properly sizing a valve is essential for ensuring optimal system performance, avoiding inefficiencies, and preventing malfunctions. The valve’s size must align with the pipeline dimensions to maintain appropriate flow rates and minimize pressure drops. Here are the key factors to consider when sizing a valve:
- Flow Coefficient (Cv): The flow coefficient (Cv) indicates the valve’s ability to allow fluid to pass through. It measures the flow rate of a fluid (in gallons per minute) that the valve can handle at a specific pressure drop. Selecting a valve with the correct Cv ensures the system can meet flow requirements without causing excessive energy losses or operational issues.
- Port Size:
- Full-Port Valves: These have an internal opening equal to the pipeline diameter, allowing fluid to flow freely without restriction. They are ideal for applications requiring maximum flow efficiency.
- Reduced-Port Valves: These have a smaller internal opening than the pipeline diameter, which can cause minor pressure drops. However, they are more compact and suitable for systems where space or weight is a concern.
Accurate sizing of valves based on these parameters helps maintain system efficiency, prevent pressure fluctuations, and ensure reliable operation across various conditions. Always consult system requirements and specifications to make the best choice.
7. Evaluate Maintenance and Durability
Long-term reliability is a critical factor in industrial applications. Consider the following:
- Ease of Maintenance: Look for valves with accessible designs for easy cleaning, repair, or part replacement.
- Material Quality: High-quality materials and coatings enhance durability, especially in harsh environments.
- Seal and Packing: Durable seals prevent leaks and ensure long-lasting performance.
Investing in a robust valve may have higher upfront costs but can save money in the long run.
8. Comply with Industry Standards
Ensure the valve meets industry-specific regulations and certifications. Examples include:
- API (American Petroleum Institute) Standards: Common in oil and gas applications.
- ANSI (American National Standards Institute) Standards: Ensure compatibility with pipeline systems.
- ISO (International Organization for Standardization) Certifications: Indicate quality and reliability.
Compliance ensures safety and smooth integration into your existing system.
9. Consult with Experts
If you’re unsure about your selection, consult with valve manufacturers, distributors, or industry experts. They can provide valuable insights and recommend valves tailored to your specific requirements.
Choose the Right Industrial Valve
Choosing the right industrial valve involves understanding your system’s operational needs, medium characteristics, and pressure/temperature requirements. By considering factors like valve type, size, material, and actuation method, you can make an informed decision that enhances efficiency, safety, and reliability.
Collaborating with experts and adhering to industry standards will further ensure that your chosen valve performs optimally for years to come.