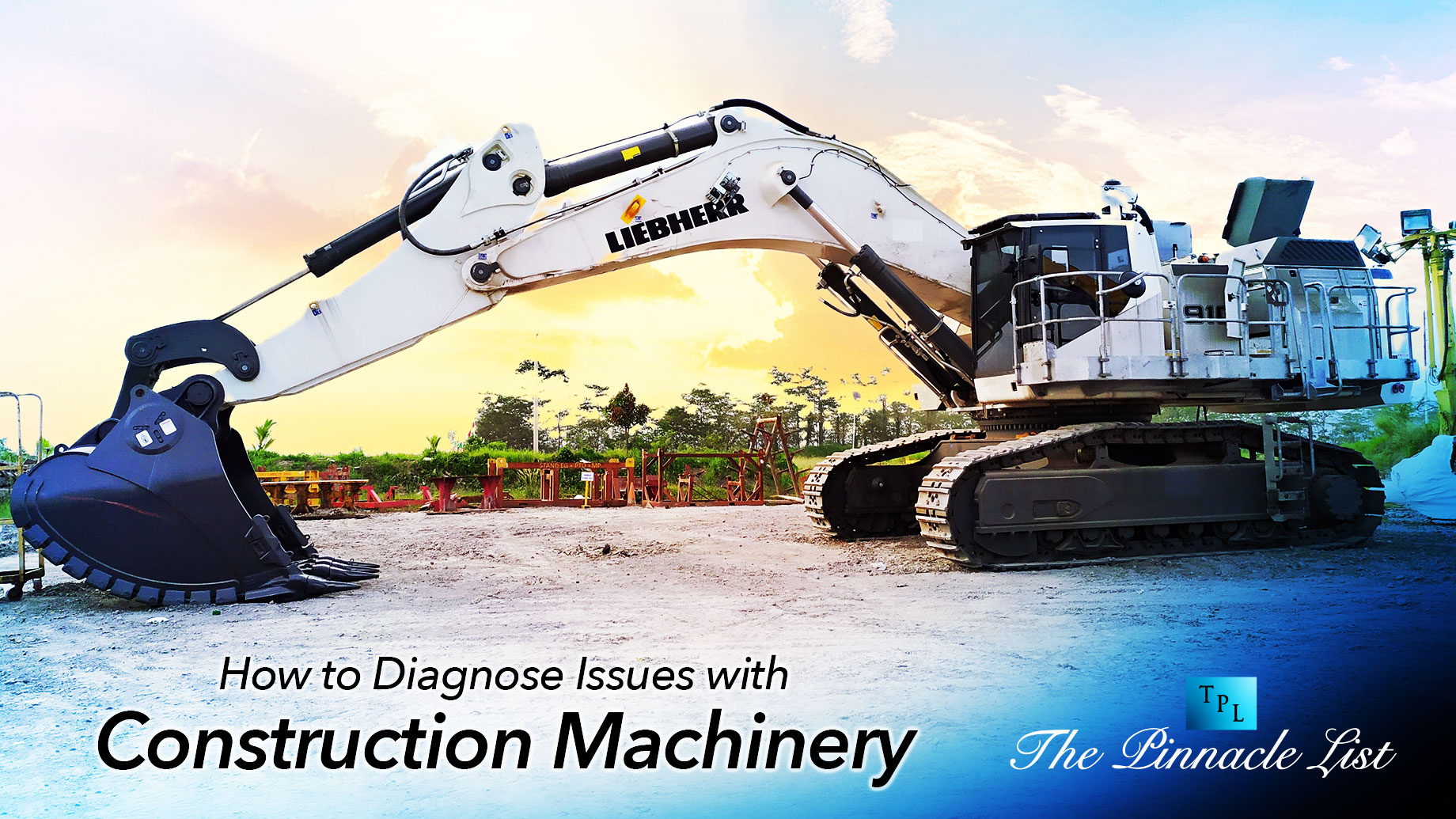
In the construction industry, machinery is the backbone that drives projects to completion. However, these robust machines are not immune to wear and tear, and diagnosing issues with them can often be a challenging task. Understanding the intricacies of construction machinery, from hydraulics to engine performance, is crucial in maintaining operational efficiency and project timelines. This document aims to provide an insightful and educational overview of how to diagnose common problems with construction machinery, empowering workers with the knowledge to tackle issues head-on and minimize potential downtime.
Visual Inspection
It is a non-invasive, straightforward approach that allows operators to identify any visible signs of damage or wear, such as leaks, cracks, or abnormalities in the machine’s structure. Additionally, closely inspecting spindle bearings, seals, hoses, fittings, and other critical components can help detect early signs of deterioration and prevent severe mechanical failures. This step is crucial because it often provides the first indication of potential problems that may require further investigation.
Moreover, regular visual inspections can help in identifying issues before they escalate into more serious problems, thereby saving time, reducing repair costs, and ensuring the machinery’s longevity. Furthermore, by conducting frequent visual inspections, one can get in touch with custom spare parts manufacturers for new parts in advance, or even decide to replace or repair the machinery if necessary. It’s worth noting that while visual inspection is essential, it’s not exhaustive, and further diagnostic processes may be needed to pinpoint the root cause of an issue.
Nonetheless, visual inspection sets the foundation for any subsequent, more comprehensive assessments of the machine’s condition.
Check Fluid Levels
Hydraulic fluid, engine oil, coolant, and brake fluid are all vital for the seamless operation of any machine. These fluids serve various purposes, such as lubrication, heat transfer, and power transmission. For instance, consistent hydraulic fluid levels are critical to guarantee the smooth functioning of the hydraulic system, whereas engine oil ensures the motor operates efficiently by reducing friction.
Similarly, coolant prevents the machine from overheating, and brake fluid is essential for safe and effective braking. Regular monitoring of these fluid levels can reveal a multitude of potential problems. Low fluid levels might indicate leaks, excessive consumption, or a failure in the system’s containment and can lead to catastrophic mechanical failures if not addressed promptly.
On the other hand, overfilled systems can also cause damage, such as blown seals or increased pressure in hydraulic systems. Hence, maintaining optimal fluid levels is not only crucial for diagnosing issues, but also for the proactive prevention of machinery problems.
Evaluate Machine Performance
This involves assessing the functioning and efficiency of the machine in its operational environment. Paying attention to any changes in the machine’s power output, fuel consumption, and overall efficiency can reveal potential issues. For instance, a sudden drop in power output could indicate problems with the engine or hydraulics, while an increase in fuel consumption might point towards inefficiencies in the engine’s combustion process.
Unusual noises or vibrations during operation can also provide valuable clues about potential mechanical issues. Moreover, modern construction machinery often comes equipped with onboard diagnostic systems that record and analyze various machine parameters, making the task of performance evaluation more precise and straightforward. These systems can alert operators to issues such as overheating, low fluid levels, or electrical faults, often before these issues result in significant performance drops.
Assess Machine Controls
Machine controls include switches, levers, and buttons used to operate the machinery, as well as electronic controls and digital interfaces in more advanced machines. These controls should respond accurately and promptly to the operator’s actions. A delayed or incorrect response can indicate a problem with the control system, such as a faulty switch, a malfunctioning sensor, or an issue with the electronic control unit (ECU). Problems with machine controls can also manifest as inconsistencies between the operator’s input and the machine’s output.
For example, if the machine moves slower than commanded, it might indicate a problem with the hydraulic system or engine performance, but it could also suggest an issue with the controls, such as a misadjusted control valve in a hydraulic system.
Utilize Diagnostic Tools
These tools range from basic handheld devices to sophisticated software that can interface directly with a machine’s onboard computer. Diagnostic tools can provide a wealth of information about a machine’s internal operations, offering insight into areas that are not typically visible or easily accessible.
For instance, they can reveal data about the engine’s performance, the status of the hydraulic system, the efficiency of the cooling system, and more. Diagnostic tools are instrumental in identifying issues that might not be immediately apparent through visual inspection or performance evaluation. They can detect abnormalities in the machine’s operations, such as irregularities in oil pressure, engine temperature, or electrical systems.
Moreover, these tools can help pinpoint the exact location and nature of a malfunction, reducing the time and effort required for troubleshooting. In more advanced machinery, diagnostic tools can read error codes generated by the machine’s onboard computer.
Consult the Machinery Manual
Often overlooked, this compendium of information provides comprehensive details about the machinery’s design, operation, maintenance, and troubleshooting procedures. It provides a roadmap of the machine’s systems and components, detailing how each part should function and interact with others. Additionally, it provides troubleshooting guides that outline common problems, their symptoms, and potential solutions. This makes it a first point of reference before escalating to more advanced diagnostic tools or specialist assistance.
Moreover, consulting the manual can prevent unnecessary damage caused by incorrect diagnostic procedures, as it provides specific instructions on safely conducting inspections and tests. Lastly, machinery manuals often contain detailed schematics and diagrams of the machine’s systems, which can aid in understanding complex machinery operations and assist in identifying unusual or problematic conditions
Seek Professional Help
Professionals in the field bring a wealth of experience, specialized knowledge, and advanced diagnostic tools to the table. Relying on professional expertise can help determine the root cause of a machinery problem more accurately and efficiently, minimizing downtime. They can interpret subtle signs of malfunction that an untrained eye might miss and implement measures to prevent the problem from recurring.
Additionally, professionals adhere to the latest safety protocols, reducing the risk of injury and further damage to the machine during the diagnostic process. Moreover, some machinery malfunctions may be symptomatic of deeper, underlying issues that only a professional can adequately identify and address.
Diagnosing issues with construction machinery involves a multifaceted approach that incorporates thorough visual inspection, performance evaluation, assessment of machine controls, utilization of diagnostic tools, consultation of the machinery manual, and seeking professional help when necessary. Each of these steps plays a vital role in identifying and addressing potential issues, helping to minimize downtime, reduce costs, and ensure the longevity and reliability of your machinery.
It is important to remember that proactive and regular maintenance and inspection are key to preventing many of the mechanical issues that can arise.