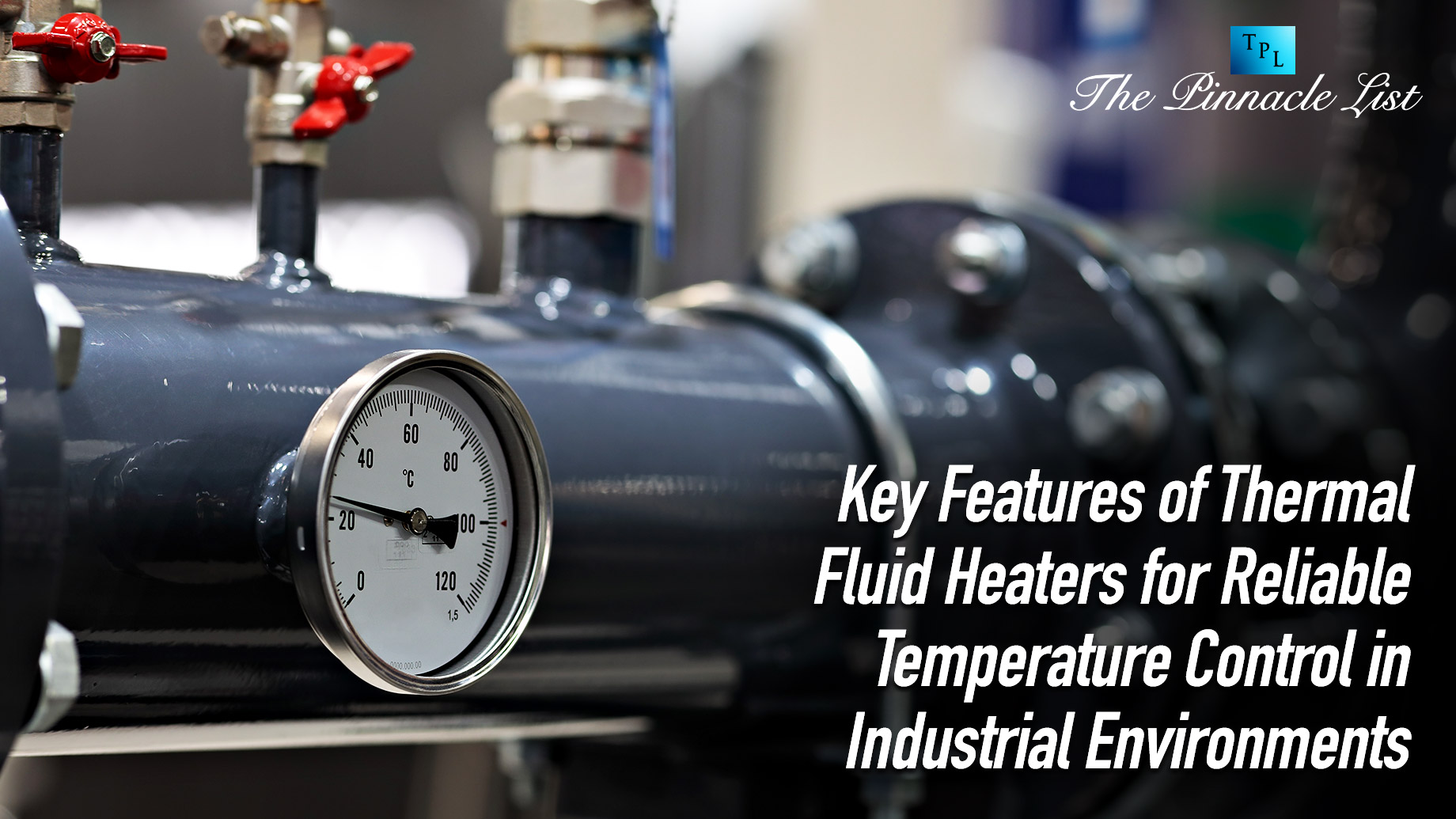
Temperature fluctuations in industries can have a major impact on the quality of the product, productivity, and maybe even the safety of the product in use, as well as the users. Thermal fluid heaters have come to be considered basic equipment in providing temperature control to industries within the pharmaceuticals, chemicals, and food processing industries. Thermal fluid heaters are meant to work under high temperatures and deliver heat energy that is reliable and flexible. This article looks at the basic aspects of thermal fluid heaters and how these heaters are used for various purposes in industries’ processes, with a special focus on the pharmaceutical equipment manufacturing industries’ advantages of using these heaters.
Thermal Fluid Heaters
Thermal fluid heaters are absolutely necessary in those branches of industry where stable temperature conditions are to be maintained. While using water and steam for heating has several advantages and disadvantages, thermal fluid heaters utilize heat transfer fluids, usually some type of oil, and can reach temperatures of up to 750°F without it being high pressure, similar to a steam heating system. This makes them suitable for use in processes that are very sensitive to temperature changes, such as chemical production, evaporation, and drying. In the pharmaceutical industry, for instance, pharmaceutical equipment manufacturers point to temperature stability as a crucial factor that determines the quality of the end formulation of the drug. Thermal fluid heaters are stable and safe solutions to heat industrial processes due to the fact they are not subjected to pressure volatility, which is essential in some applications. Moreover, they do not experience pressure rise as the temperature increases, thus applying in a broad spectrum of production conditions, including low temperatures and high-temperature operations, hence improving the flexibility of operations in industrial processes.
Characteristics of Thermal Fluid Heaters
Many thermal fluid heaters are equipped with special functionalities that make them appropriate for operation at the industrial level. They are able to heat food to high temps with low pressure thus making safety much easier to achieve and system stress a lot much less. Current thermal fluid heaters have developed and integrated sophisticated control systems to monitor and regulate temperature, flow rate, and heat level, which is equally important for uniformity. Some also have a backup power feature that keeps the generator on in the event of another unit failing. These features are especially preferred in industries where the heating process has to be continuous, such as the pharmaceutical and chemical sectors. Many thermal fluid heaters are jointly designed for the manufacturers of pharmaceutical equipment as required to have optimal productivity, which also complies with the standards of the industry. Furthermore, the structure of these heaters enables them to be interfaced with facility management systems-installing them as part of the existing systems so that adjustments can be made remotely at certain time intervals depending on the environment in order to optimize the use of the heaters.
Energy Savings and Costs
The best thing about thermal fluid heaters is their fuel consumption efficiency, which correlates directly to the cost of operating the industrial process. Used at lower pressures than steam boilers, thermal fluid heaters utilize a lesser amount of energy and are, therefore, cheaper to operate and more friendly to the environment than other conventional thermal boilers. They also suffer less mechanical wear meaning that they have decreased maintenance time and losses due to machine breakdowns. The heat transfer fluids utilized in these systems have high thermal inertia and allow for a fast exchange of temperature, but without significant fluctuations in energy. This efficiency has its greatest value in large shops where heating is quite an expensive process in the ordinary course. Due to these reasons, it is often advised by manufacturers of the pharmaceutical equipment that thermal fluid heaters are cheap to use while maintaining the high quality standards hence can be relied on in the current competitive industrial markets without necessarily having to part ways with a lot of cash to cater for the bills that may be incurred by the use of other types of heaters. Moreover, thermal fluid heaters incorporate features like the speed of the pump as a frequency drive (VFDs) to regulate the flow of pump electricity during off-peak periods; and heat recovery systems, thereby reducing overall costs by reusing waste heat.
Safety and Environmental Considerations
Safe operation of any industrial equipment is always a concern, as well as environmental impact, and thermal fluid heaters meet these standard requirements. They work at much lower pressures than the steam systems, so any occurrences of pressure-related problems, for example, explosions, are eliminated. This makes them suitable for areas where high-temperature processes are common so as to avoid failure. Moreover, present-day thermal fluid heaters also have protections, including leakage detection and protection, auto-stop mechanism, as well as emergency cooling to boost the safety of operators. Other features that have received consideration are emissions, though most manufacturers now design burners with low emissions and manufacture energy-efficient heat recovery systems. China’s thermal fluid heater manufacturers also pay much attention to environmental protection and strive to make themselves and their products environmentally friendly, which makes thermal fluid heaters safe and environmentally friendly heating equipment for industries that want to reduce CO2 emissions while pursuing high safety standards. Some of the heaters also come with environmentally friendly heat transfer fluids that make the plants achieve their green goals.
Versatility in Applications Across Industries
Thermal fluid heaters are quite flexible, so they can be used for a number of industry applications. In the pharmaceutical and chemical industry, they enable highly accurate temperature control in reactor heating, distillation, and solvent recovery. When used in the food and beverage industry, they are useful in processes that involve heating and have tight control over temperature standards of pasteurization, cooking, and drying procedures. The plastics and textiles industries also find the use of thermal fluid heaters in molding, extruding, and drying processes. This versatility is also useful when one heating system needs to be used in several applications, preventing the need for multiple systems. The manufacturers of pharmaceutical equipment always advise clients with multiple heating requirements to use thermal fluid heaters, commonly referred to as increasing their customer value by serving multiple operations within a single industry. Moreover, they are designed to work within different protocols typical for various sectors, so these heaters will suit both general and specific application needs.